A 3D printed titanium structure with incredible strength may change how we make things from medical implants to aircraft.
RMIT University researchers have used titanium alloy to create a new metamaterial – a term referring to an artificial material with qualities that do not exist naturally. According to a report in the Journal of Advanced Materials, the material could revolutionise the manufacturing of several important products due to its unique lattice structure.
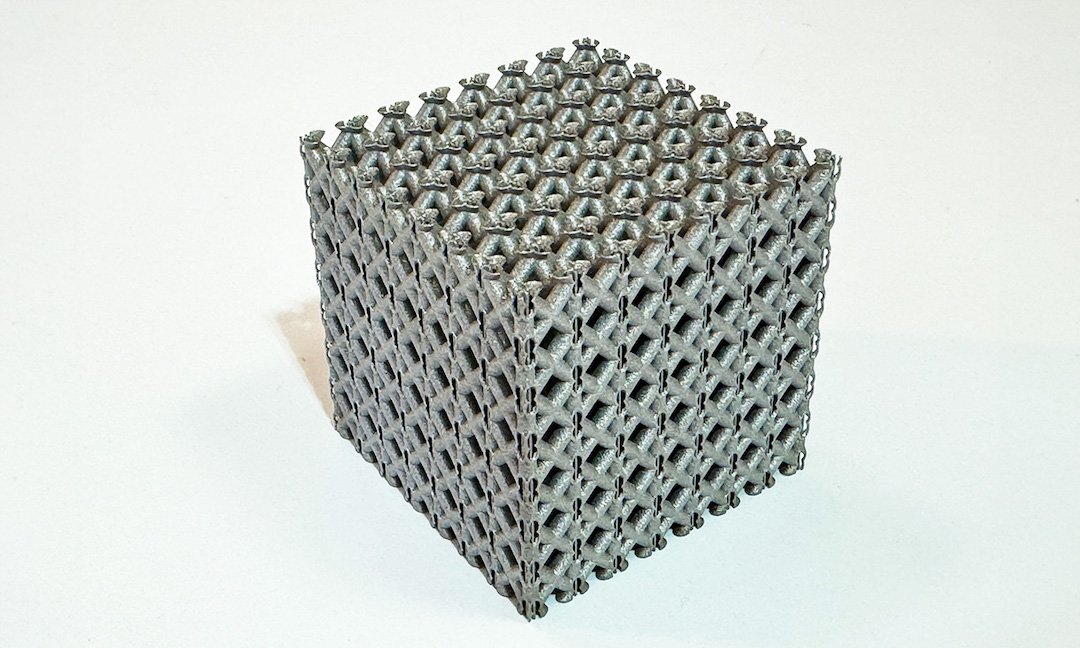
The 3D printed titanium lattice structure
A test of strength
The researchers on this groundbreaking project drew their inspiration from strong hollow-stemmed plants such as the Victorian water lily or the hardy organ pipe coral, which are a perfect combination of lightness and strength. It was through study of these flora that the lattice design made of hollow struts was first conceived.
According to RMIT’s Distinguished Professor Ma Qian, the process of trying to replicate these hollow ‘cellular structures’ was complex, with issues such as manufacturability and load stress resulting in many failed tests.
“Ideally, the stress in all complex cellular materials should be evenly spread,” Qian explained.
“However, for most topologies, it is common for less than half of the material to mainly bear the compressive load, while the larger volume of material is structurally insignificant.”
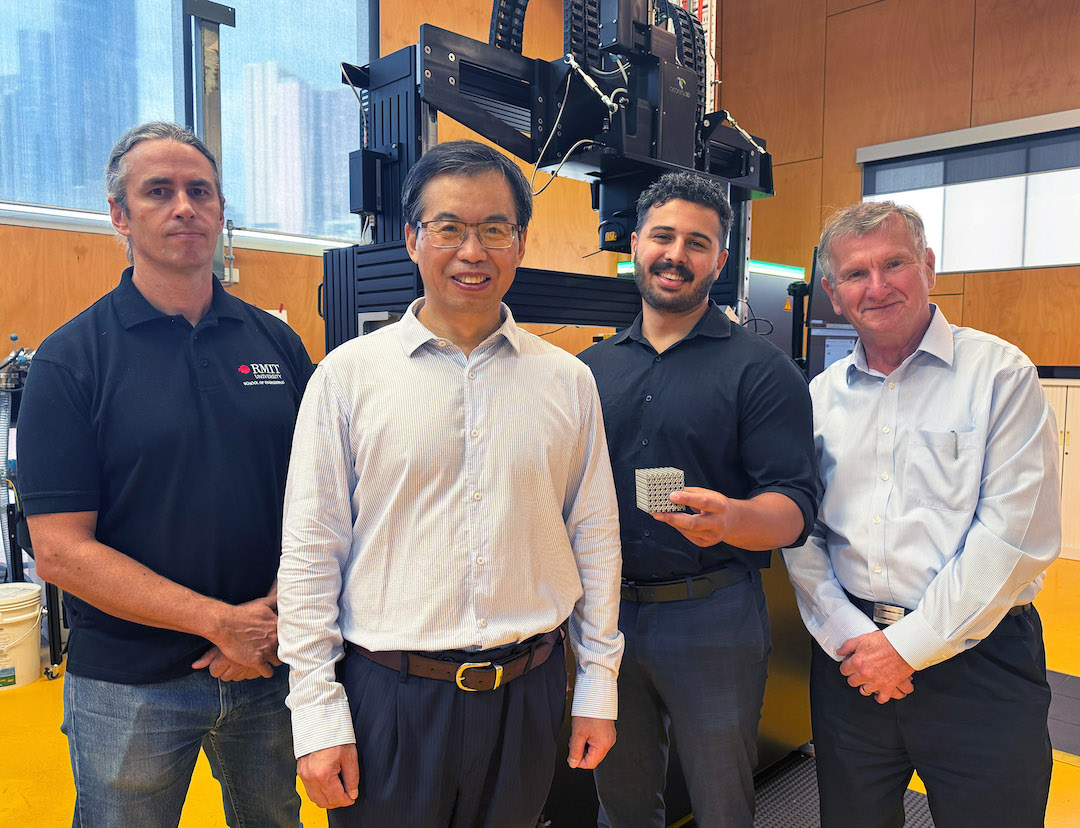
The team: Professor Martin Leary, Distinguished Professor Ma Qian, Jordan Noronha and Distinguished Professor Milan Brandt.
Printing practice
In order to overcome these structural challenges, researchers turned to metal 3D printing.
“We designed a hollow tubular lattice structure that has a thin band running inside it. These two elements together show strength and lightness never before seen together in nature,” said Qian.
“By effectively merging two complementary lattice structures to evenly distribute stress, we avoid the weak points where stress normally concentrates.”
The design was printed using laser powder bed fusion, which melts layers of metal powder together using high powered laser beams.
Through rigorous testing, it was determined that the printed design was 50 percent stronger than cast magnesium alloy, the strongest alloy used in aerospace engineering.
The clever structure halved the amount of stress on the weak points of the lattice, and deflected cracks along the structure, making it useful for applications in a variety of fields.
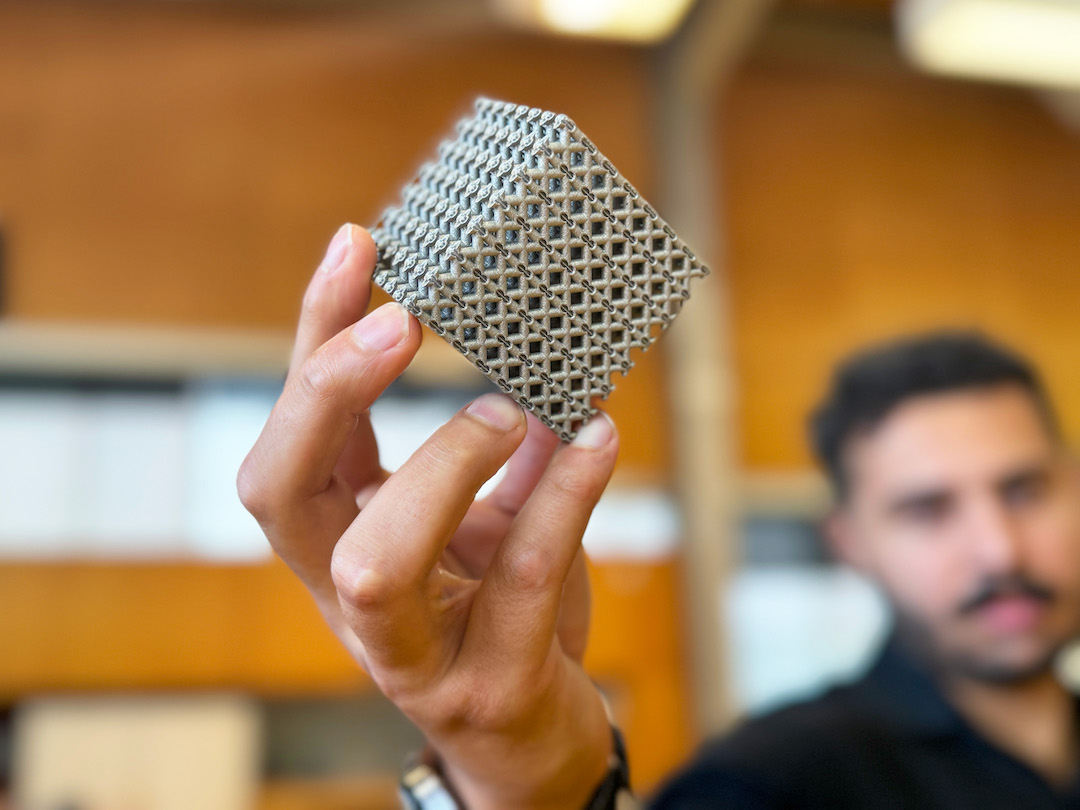
Study lead Jordan Noronha with the titanium lattice cube.
Breaking new ground
According to study lead author and RMIT PhD candidate Jordan Noronha, this project could be repeated on small or large scales by employing different printers. This printability, as well as the strength, biocompatibility and heat and corrosion resistance make it a useful material for medical devices and rocket parts.
“Compared with the strongest available cast magnesium alloy currently used in commercial applications requiring high strength and lightweight, our titanium metamaterial with a comparable density was shown to be much stronger or less susceptible to permanent shape change under compressive loading, not to mention more feasible to manufacture,” Noronha said
In order to expand its applications, the team is attempting to increase the heat resistance of the material from 350 degrees celsius to 600 degrees celsius. However, they acknowledge that there are some challenges still in their way.
“Traditional manufacturing processes are not practical for the fabrication of these intricate metal metamaterials, and not everyone has a laser powder bed fusion machine in their warehouse,” explained Noronha.
“However, as the technology develops, it will become more accessible and the printing process will become much faster, enabling a larger audience to implement our high-strength multi-topology metamaterials in their components. Importantly, metal 3D printing allows easy net shape fabrication for real applications.”
To read about sustainability in the steel industry, click here.